What is Porosity in Welding: Best Practices for Preventing Porous Welds
What is Porosity in Welding: Best Practices for Preventing Porous Welds
Blog Article
Unraveling the Secret of Porosity in Welding: Tips for Minimizing Problems and Taking Full Advantage Of Quality
In the detailed globe of welding, porosity continues to be a relentless obstacle that can substantially affect the high quality and stability of welded joints. As we delve right into the midsts of porosity in welding, discovering the keys to its prevention and control will be paramount for specialists looking for to understand the art of high-quality weldments.
Comprehending Porosity in Welding
Porosity in welding, an usual problem come across by welders, refers to the visibility of gas pockets or spaces in the bonded product, which can compromise the integrity and top quality of the weld. These gas pockets are normally caught during the welding procedure because of numerous aspects such as incorrect securing gas, polluted base products, or inaccurate welding parameters. The development of porosity can weaken the weld, making it at risk to splitting and corrosion, eventually leading to architectural failings.
By acknowledging the value of keeping correct gas securing, ensuring the cleanliness of base materials, and optimizing welding settings, welders can significantly reduce the likelihood of porosity formation. Overall, a comprehensive understanding of porosity in welding is important for welders to produce premium and resilient welds.
Usual Sources Of Porosity
When inspecting welding processes for possible quality concerns, comprehending the typical reasons of porosity is crucial for preserving weld honesty and avoiding architectural failures. Porosity, defined by the visibility of cavities or spaces in the weld steel, can considerably jeopardize the mechanical residential or commercial properties of a bonded joint.
An additional prevalent cause of porosity is the visibility of dampness and contaminants externally of the base steel or filler product. When welding materials are not correctly cleaned up or are revealed to high degrees of humidity, the vaporization of these contaminants during welding can create gaps within the weld bead. Additionally, welding at incorrect specifications, such as exceedingly high traveling rates or currents, can create excessive turbulence in the weld pool, trapping gases and causing porosity. By dealing with these typical reasons with appropriate gas securing, product prep work, and adherence to ideal welding specifications, welders can decrease porosity and boost the top quality of their welds.
Strategies for Porosity Avoidance
Carrying out efficient safety nets is crucial in reducing the occurrence of porosity in welding procedures. One method for porosity prevention is making certain correct cleaning of the base steel prior to welding. Contaminants such as oil, oil, corrosion, and paint can result in porosity, so thorough cleansing utilizing additional reading appropriate solvents or mechanical approaches is vital.

Using high-grade filler materials and protecting gases that are ideal for the base steel and welding process can substantially lower the risk of porosity. Furthermore, keeping correct welding parameters, such as voltage, present, take a trip rate, and gas circulation price, is vital for porosity prevention.
Additionally, using correct welding strategies, such as maintaining a consistent travel speed, electrode angle, and arc size, can help stop porosity (What is Porosity). Ample training of welders to ensure they follow best practices and quality control procedures is also vital in lessening porosity issues in welding

Ideal Practices for Top Quality Welds
One secret practice is preserving proper sanitation in the welding area. Extensively cleaning up the work surface and surrounding location before welding can aid reduce these concerns.
An additional ideal technique is to carefully select the appropriate welding parameters for the specific materials being joined. Correct criterion option ensures optimum weld infiltration, blend, and total high quality. Utilizing top notch welding consumables, such as electrodes and filler steels, can substantially affect the why not check here final weld quality.
Importance of Porosity Control
Porosity control plays an essential role in ensuring the honesty and high quality of welding joints. Porosity, defined by the presence of cavities or gaps within the weld metal, can significantly endanger the mechanical properties and architectural stability of the weld. Excessive porosity damages the weld, making it a lot more vulnerable to cracking, deterioration, and overall click for info failing under operational loads.
Effective porosity control is crucial for maintaining the wanted mechanical residential or commercial properties, such as toughness, ductility, and strength, of the bonded joint. What is Porosity. By decreasing porosity, welders can improve the general top quality and reliability of the weld, making sure that it fulfills the performance demands of the desired application
Furthermore, porosity control is important for accomplishing the wanted aesthetic appearance of the weld. Extreme porosity not just damages the weld but also diminishes its aesthetic allure, which can be critical in industries where looks are essential. Proper porosity control techniques, such as utilizing the right protecting gas, regulating the welding criteria, and making certain proper cleanliness of the base materials, are important for producing premium welds with very little flaws.
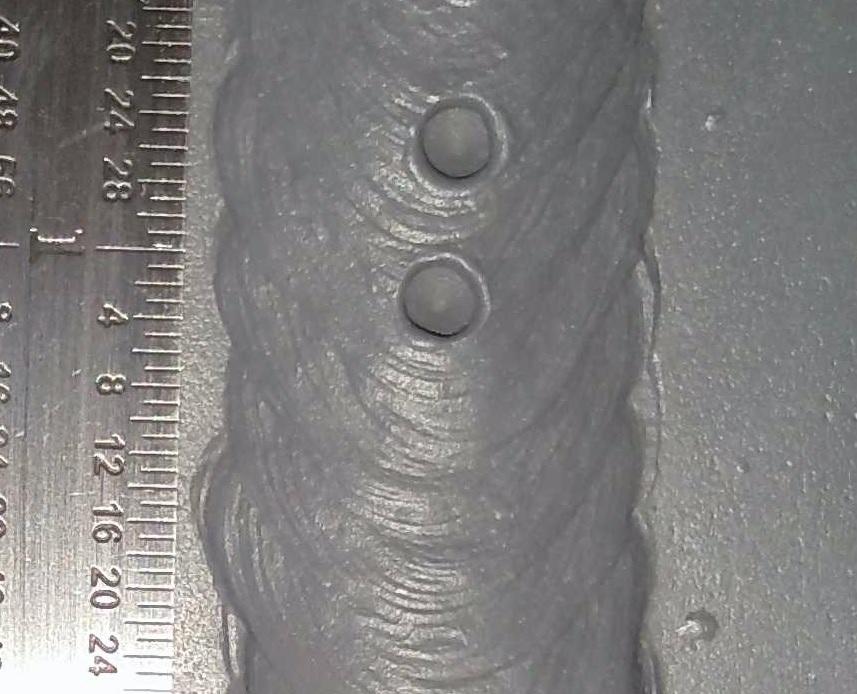
Conclusion
In conclusion, porosity in welding is a typical defect that can compromise the quality of the weld. By comprehending the reasons for porosity and applying correct prevention techniques, welders can lessen flaws and accomplish better welds. It is crucial to regulate porosity in welding to ensure the honesty and toughness of the last product. Implementing best techniques for porosity control is vital for accomplishing optimal welding outcomes.
Report this page